CFD Analysis of Axial Fan: Computational Fluid Dynamics (CFD) has revolutionized the way engineers approach the design and optimization of various mechanical systems. In this article, we will delve into the world of CFD analysis, focusing specifically on the application of CFD in the evaluation and improvement of axial fans. Axial fans play a crucial role in numerous industries, and understanding how CFD can enhance their performance is paramount.
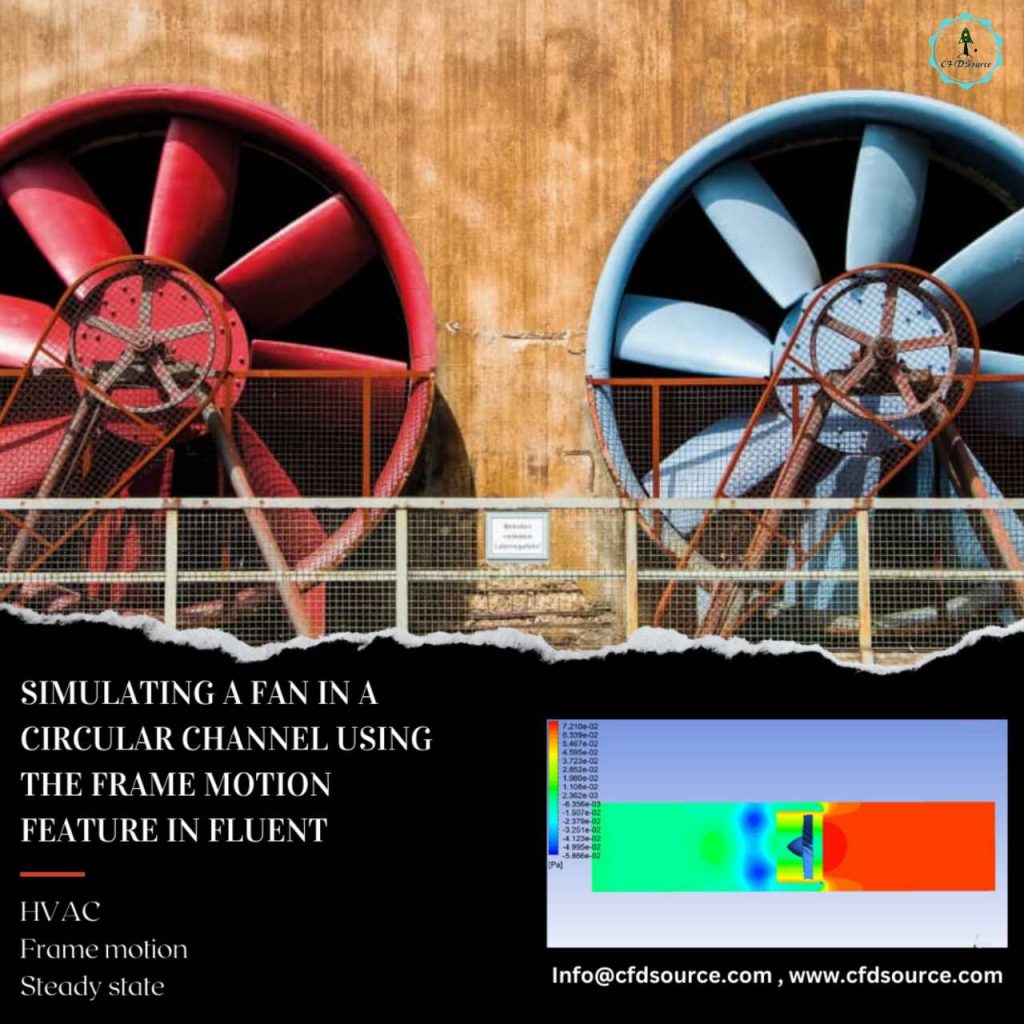
Introduction
Computational Fluid Dynamics (CFD) has emerged as a powerful tool in the field of engineering, enabling us to delve deep into the intricate world of fluid dynamics without the need for physical prototypes. It has revolutionized the way we design and optimize various mechanical systems, and its application in the evaluation and enhancement of axial fans is no exception. CFD is, at its core, a numerical approach that allows us to simulate, analyze, and predict the behavior of fluids and gases in complex systems.
This article explores the profound impact of CFD in the realm of axial fans, delving into its importance, applications, and the fundamental principles that make it an indispensable resource in modern engineering. In the context of axial fans, CFD analysis plays a pivotal role in improving performance, reducing noise, ensuring safety, and enhancing efficiency. This article will take you on a journey through the fascinating world of CFD analysis as it relates to axial fans.
Understanding Axial Fans
To comprehend the significance of CFD analysis in the realm of axial fans, it’s essential to first grasp the basics of these devices. Axial fans are a common sight in many industrial and commercial applications, from cooling systems in data centers to aircraft engines. They are characterized by their design, featuring a series of blades that rotate around a central axis, creating a flow of air parallel to the shaft.
This unique design allows axial fans to generate high airflow at relatively low pressures. In essence, they’re highly efficient at moving air, which makes them invaluable in scenarios where the goal is to circulate or ventilate large volumes of air. Understanding the working principles of axial fans is essential to appreciate the significance of CFD analysis, which aids in optimizing their performance and efficiency.
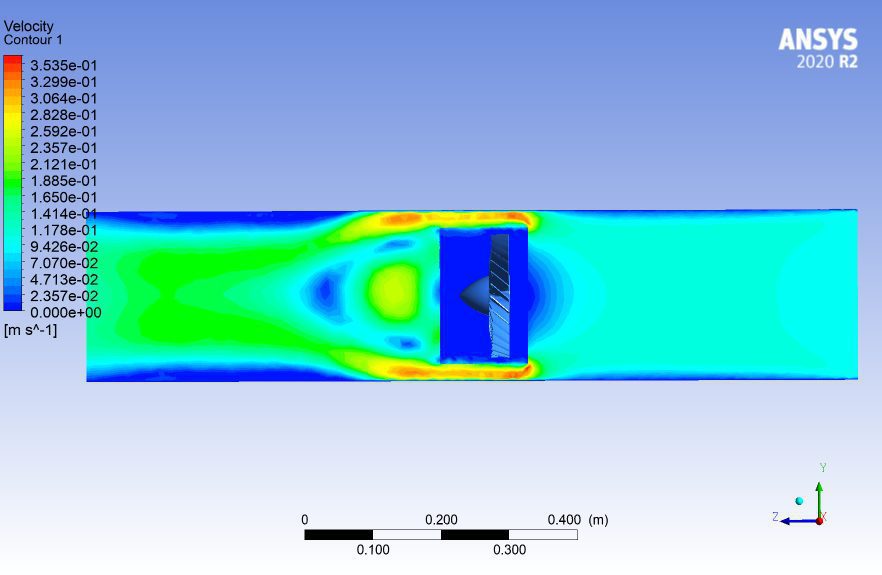
Importance of CFD in Axial Fan Design
The importance of CFD in axial fan design cannot be overstated. In the context of designing these critical components, CFD serves as a virtual testing ground, allowing engineers to visualize and predict how air flows through the fan, identify areas of turbulence, and assess factors such as pressure distribution and temperature changes.
The ability to simulate the behavior of fluids and gases within the fan is a game-changer. With CFD, engineers can experiment with different designs, test the impact of changes, and ultimately fine-tune the fan for optimal performance. It’s not just about maximizing airflow; it’s also about reducing noise, ensuring safety by preventing potential issues like overheating, and improving energy efficiency. In essence, CFD analysis provides the insights necessary to create axial fans that meet or exceed performance expectations.
Basics of CFD Analysis
To embark on a journey of CFD analysis, one must first understand the fundamental principles that underpin this computational tool. CFD is based on the numerical solution of the governing equations that describe fluid flow. These equations, known as the Navier-Stokes equations, are complex mathematical models that define how fluids move, and solving them accurately is the essence of CFD. The process involves discretizing the computational domain into smaller cells, which allows us to approximate the continuous fluid behavior. The most commonly used numerical methods include finite element analysis, finite volume analysis, and finite difference analysis.
These methods enable us to convert the partial differential equations of fluid dynamics into algebraic equations that can be solved iteratively using high-performance computing hardware. In other words, CFD analysis is about breaking down a complex fluid flow problem into smaller solvable parts, crunching the numbers, and reassembling the solution to visualize the behavior of fluids in intricate systems. This fundamental understanding is vital as it sets the stage for the application of CFD in axial fan design and optimization.
Preparing for CFD Analysis
Before the magic of CFD analysis can be harnessed, a series of meticulous steps must be taken in preparation. Engineers embark on a data gathering mission, collecting information about the axial fan’s geometry, operating conditions, and the physical environment in which it operates. This data forms the foundation of the CFD analysis, providing essential input parameters. The next crucial step involves creating a digital representation of the fan’s geometry, a process known as modeling. The geometric model serves as the computational domain for the analysis. Here, the fan, its surroundings, and any relevant components are meticulously represented.
Setting up the computational domain, complete with boundary conditions, is an intricate dance of defining the problem’s boundaries and constraints. This is where engineering acumen and CFD expertise intertwine, as selecting the right boundary conditions and making informed assumptions are critical to the analysis’s accuracy. The preparation stage is where all the essential building blocks for a successful CFD analysis come together, ensuring that the virtual testing ground is as close to reality as possible, and that the results will yield meaningful insights into the axial fan’s performance.
Performing CFD Simulations
With the groundwork laid during the preparation phase, engineers move on to the heart of CFD analysis: performing simulations. In this step, they transform the real-world fan and its operating conditions into a virtual environment, where the laws of fluid dynamics apply. The governing equations, particularly the Navier-Stokes equations, are solved using numerical methods. To do this, engineers turn to specialized CFD software packages that can handle the complexity of the calculations.
These software programs use algorithms and solvers to compute how air or other fluids behave within the fan. The analysis might take seconds, hours, or even days, depending on the complexity of the problem and the available computational resources. Solving these equations requires substantial computing power, and iterative processes often ensue to refine the results. The simulation reveals intricate details about the airflow, pressure distribution, and temperature profiles within the axial fan, offering engineers the ability to see the invisible and understand the ineffable.
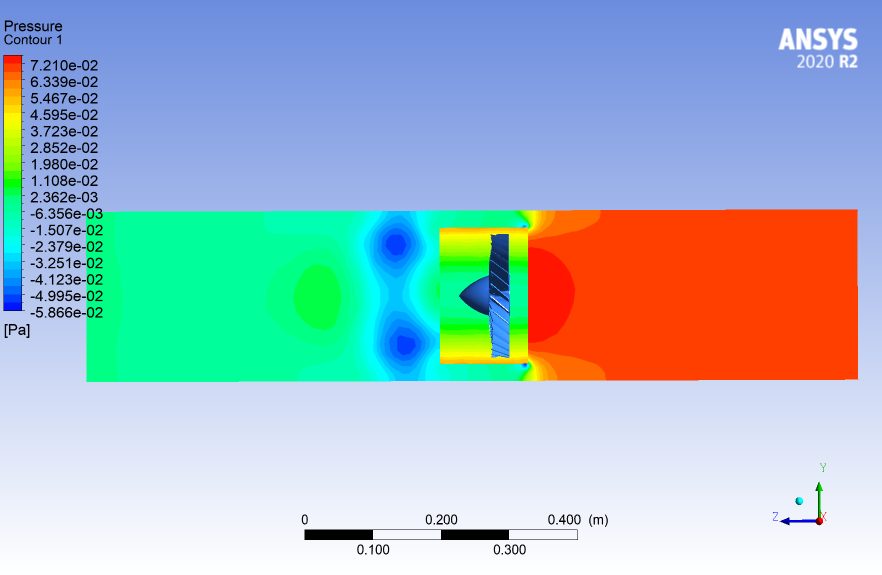
Key Parameters Analyzed
In the realm of CFD analysis for axial fans, several key parameters and variables come under the microscope. First and foremost, engineers scrutinize the pressure distribution within the fan. Understanding how pressure varies throughout the fan is crucial in assessing its performance and efficiency. Additionally, velocity profiles are meticulously studied to determine the airflow patterns and identify areas of turbulence or separation. The temperature changes within the fan are also a focal point, as overheating can be a serious concern.
CFD provides a means to identify temperature variations and make adjustments accordingly. Turbulence modeling is another critical aspect of CFD analysis. Turbulence can have a significant impact on fan performance and energy efficiency, so engineers employ various turbulence models to predict and mitigate its effects. These parameters offer a holistic view of the fan’s behavior and allow for data-driven decisions on design improvements.
Challenges and Limitations of CFD Analysis
Despite the incredible capabilities of CFD analysis, it is not without its challenges and limitations. One prominent challenge is the necessity to make certain assumptions and simplifications during the analysis. These assumptions can affect the accuracy of the results and may not fully capture all the intricacies of the real-world system. Another hurdle is the substantial computational resources and time required for complex simulations. High-performance computing clusters are often necessary for intricate problems, and even with such resources, simulations can take a considerable amount of time. Additionally, validating and verifying the results is a crucial step.
It’s essential to ensure that the virtual simulation accurately reflects real-world behavior, which can be a complex process in itself. Furthermore, not all fluid dynamics problems can be solved using CFD. Highly complex, multi-phase, and chaotic flows can be challenging for CFD software to handle. In such cases, other experimental or analytical methods may be necessary to complement CFD analysis. Understanding these challenges and limitations is vital for engineers to make informed decisions and interpret the results within the proper context.
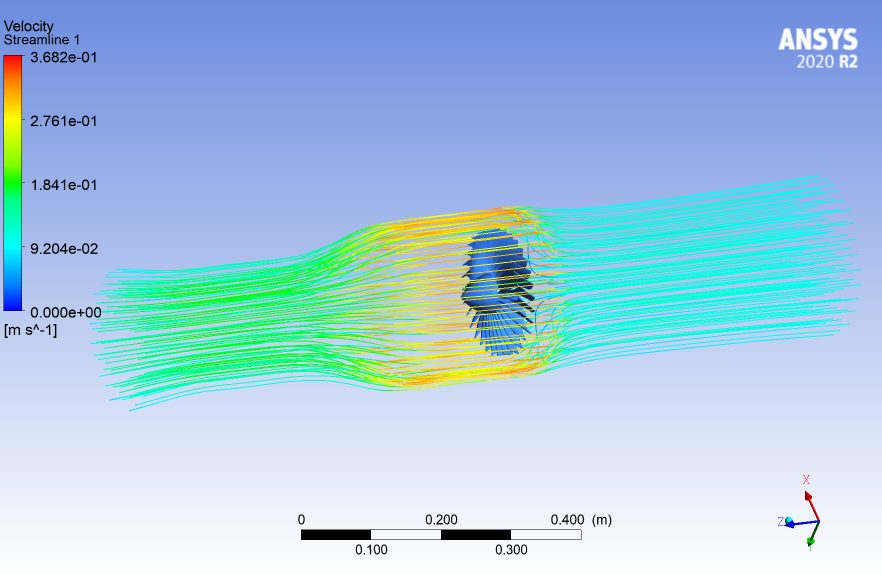
Case Study: CFD Analysis of an Axial Fan
To illustrate the practical application of CFD analysis, we will delve into a compelling case study involving a specific axial fan. This case study serves as a real-world example of how CFD can be used to enhance fan performance. In this scenario, we have a well-defined axial fan used in an industrial cooling system. The fan’s performance had been suboptimal, leading to increased energy consumption and concerns about overheating. Engineers embarked on a journey to leverage CFD to transform the fan’s performance. The first step was to gather data about the fan, including its geometry, operating conditions, and the surrounding environment. This data was meticulously input into the CFD software to create a digital model of the fan and its surroundings.
The boundary conditions were defined, assumptions were made, and the simulation was initiated. As the CFD analysis unfolded, engineers could visualize the airflow within the fan. The pressure distribution was analyzed, revealing areas of inefficiency. Velocity profiles exposed regions of turbulence, and temperature changes were pinpointed. Armed with these insights, the engineers made design modifications, such as adjusting blade angles and optimizing the fan’s shape. The simulation was iteratively improved, and the results were compared to real-world measurements. In the end, the axial fan’s performance was significantly enhanced, reducing energy consumption and mitigating concerns of overheating. This case study exemplifies how CFD can transform a mechanical system’s performance and demonstrates its real-world impact.
Real-World Applications
The real-world applications of CFD analysis in the context of axial fans are diverse and impactful. One notable domain where CFD is instrumental is in Heating, Ventilation, and Air Conditioning (HVAC) systems. These systems rely heavily on axial fans to circulate air, and the efficient functioning of these fans is critical for maintaining indoor air quality and temperature control. CFD allows HVAC engineers to optimize fan designs to ensure even airflow distribution, minimal noise, and energy efficiency. Furthermore, axial fans play a vital role in the aerospace industry, especially in the engines of aircraft.
CFD analysis assists in improving the performance and safety of these fans, reducing noise, and enhancing fuel efficiency. The automotive industry also benefits from CFD analysis, as it helps design efficient cooling systems for engines and brakes. In this context, CFD allows engineers to address issues related to overheating and thermal management. CFD’s real-world applications extend to industries where airflow and fluid dynamics are critical, and its role in improving axial fan performance cannot be understated.
Conclusion
CFD Analysis of Axial Fan: In conclusion, the integration of Computational Fluid Dynamics (CFD) into the design and optimization of axial fans has revolutionized the field of mechanical engineering. This article has provided an in-depth exploration of the applications of CFD in understanding axial fans, revealing the significance of CFD in the design process. It has covered the fundamentals of CFD analysis, the preparation required, the intricacies of performing simulations, and the key parameters analyzed during the process. Challenges and limitations inherent to CFD analysis have been discussed, ensuring that engineers are well-prepared to navigate the complexities of real-world applications.
Through a compelling case study, we witnessed the transformative power of CFD in enhancing axial fan performance. Furthermore, this article highlighted the diverse real-world applications of CFD, from HVAC systems to aerospace and automotive engineering. As we gaze into the future, it is evident that CFD analysis is on the cusp of groundbreaking transformations, with AI, ML, software advancements, and expanding applications leading the way. The implications of these trends are profound, promising to make CFD analysis more accessible and impactful in a wide range of industries. The journey of CFD is one of continuous innovation, and its role in shaping our world’s engineering landscape is far from over.