CFD Analysis of Heat Exchanger: Heat exchangers play a vital role in various industrial processes, from heating and cooling systems to power generation and chemical manufacturing. Ensuring their efficiency is crucial to save energy and reduce operational costs. Computational Fluid Dynamics (CFD) analysis is a powerful tool for evaluating and optimizing heat exchanger performance. In this essay, we will delve into the world of CFD analysis for heat exchangers, exploring its principles, applications, and significance.
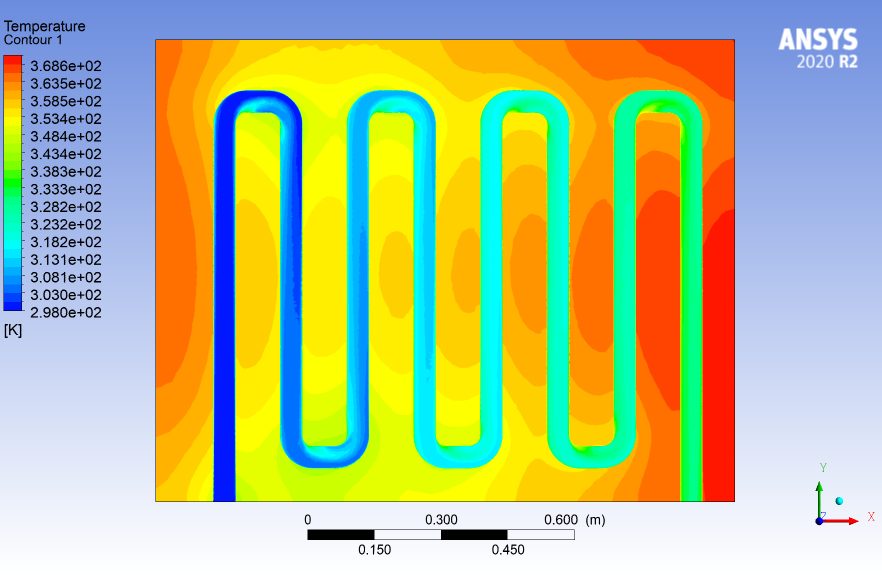
Understanding Heat Exchangers
Heat exchangers are ubiquitous in modern industrial processes and everyday life, yet their significance often goes unnoticed. These devices, available in various shapes and sizes, serve the fundamental purpose of transferring thermal energy between two or more fluids. Whether in your car’s radiator, the air conditioning system at your workplace, or the heat recovery unit in a power plant, heat exchangers play a pivotal role in maintaining temperature control.
The underlying principle is simple: they allow two different fluids to come into close contact without mixing, ensuring that one fluid’s heat is transferred to the other. This transfer can either involve heating the cold fluid or cooling the hot fluid, depending on the application. For example, in a car’s radiator, hot engine coolant flows through the heat exchanger, transferring its heat to the surrounding air to keep the engine from overheating. Conversely, in a heating system, cold air passes over a heat exchanger to be warmed before circulating through a building. This seamless exchange of heat is what makes heat exchangers essential in a wide array of industries.
Importance of Heat Exchanger Efficiency
In a world where energy efficiency and sustainability are paramount, the efficiency of heat exchangers cannot be overstated. An inefficient heat exchanger can lead to excessive energy consumption, higher operational costs, and even environmental repercussions. Consider your home’s HVAC system; an inefficient heat exchanger could result in higher electricity bills and increased carbon emissions, impacting both your wallet and the environment. Therefore, the importance of optimizing heat exchanger efficiency cannot be overstated. Energy is a precious resource, and conserving it has become a global imperative. Efficient heat exchangers are instrumental in this endeavor.
They can recover heat from exhaust gases or other waste streams, reusing it to preheat incoming fluids, thereby reducing the energy required to bring those fluids to the desired temperature. This has a direct impact on energy consumption and cost savings, which is particularly significant in large-scale industrial operations. Therefore, industries worldwide strive to enhance heat exchanger efficiency, not only for financial reasons but also to meet sustainability goals and reduce their carbon footprint.
How CFD Analysis Works
Computational Fluid Dynamics (CFD) analysis is a powerful technique for simulating and understanding the behavior of fluids and heat transfer within heat exchangers. It’s a bit like having a crystal ball that allows engineers to peer into the heart of a heat exchanger’s operation without the need for expensive and time-consuming physical prototypes. CFD analysis involves solving a set of mathematical equations that describe fluid flow and heat transfer.
These equations are complex and require high-performance computing resources to solve. However, once solved, they provide a wealth of information about the flow patterns, temperature distributions, and pressure gradients inside the heat exchanger. It’s akin to creating a virtual laboratory where engineers can experiment with different scenarios, varying parameters like flow rates, fluid properties, and geometry. This level of detail is invaluable in optimizing heat exchanger performance.
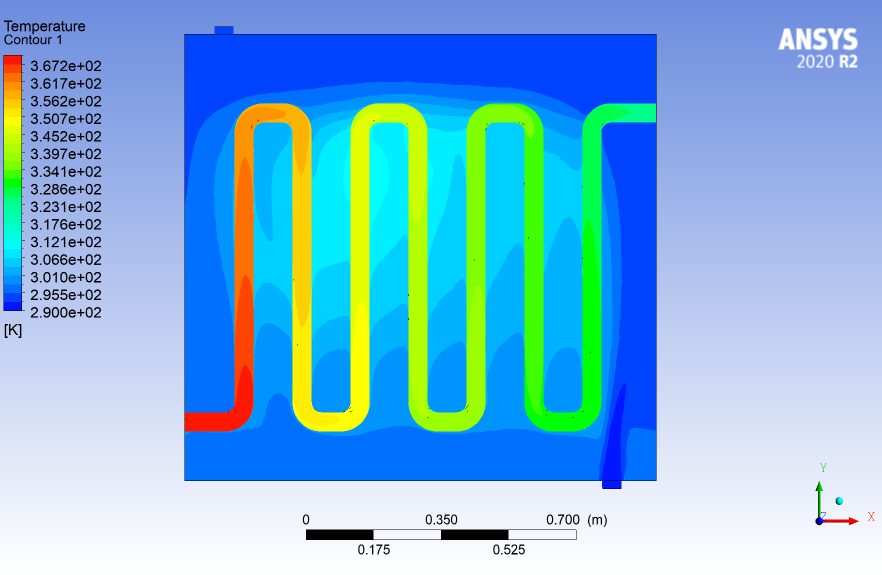
Benefits of CFD Analysis in Heat Exchangers
The benefits of employing CFD analysis in the realm of heat exchangers are manifold. First and foremost, it provides engineers with a deep understanding of how fluids behave within the heat exchanger, giving them insights into the intricacies of the system. This information is invaluable for decision-making, as it allows for data-driven modifications that enhance efficiency. CFD simulations enable engineers to experiment with different designs and operational conditions virtually, saving time and resources compared to traditional trial-and-error methods. Furthermore, CFD analysis offers a level of detail that is nearly impossible to achieve with physical experiments.
It allows for the examination of temperature and velocity distributions at various points within the heat exchanger, pinpointing areas of potential improvement. Engineers can also assess the impact of design changes on heat exchanger performance. In addition to efficiency gains, CFD analysis contributes to cost reduction, as it helps avoid unnecessary physical prototypes and minimizes the need for expensive experiments. This approach is particularly advantageous when dealing with high-temperature and high-pressure systems, where safety is a concern. Overall, CFD analysis is a game-changer in the field of heat exchangers, offering a more comprehensive, efficient, and cost-effective path to optimization.
Benefits of CFD Analysis in Heat Exchangers
The application of Computational Fluid Dynamics (CFD) analysis in the context of heat exchangers offers a plethora of benefits, making it an indispensable tool in the field of thermal engineering. First and foremost, CFD analysis provides engineers with insights into flow patterns, temperature distributions, and pressure gradients within the heat exchanger. By visualizing these factors, engineers can identify potential areas of improvement. For example, in a shell-and-tube heat exchanger, CFD analysis can reveal uneven temperature distribution or areas of recirculation that may hinder efficient heat transfer. Armed with this knowledge, engineers can make informed decisions on design modifications or operational adjustments to optimize the heat exchanger’s performance.
One of the greatest advantages of CFD analysis is its ability to simulate various scenarios without the need for physical prototypes. Engineers can virtually experiment with different parameters, such as flow rates, materials, and geometry, to assess their impact on the heat exchanger’s efficiency. This virtual laboratory provides a cost-effective and time-efficient means of testing and fine-tuning the heat exchanger’s design. Additionally, it allows for the exploration of performance under a wide range of operating conditions, which is crucial in industries where factors like temperature, pressure, and fluid properties can vary significantly.
The fine level of detail offered by CFD analysis is unmatched by traditional experimental methods. Engineers can examine temperature and velocity distributions at various points within the heat exchanger, enabling them to pinpoint precisely where improvements are needed. This level of specificity is invaluable when dealing with intricate heat exchanger designs or when striving for the highest possible efficiency. Moreover, CFD simulations can be instrumental in understanding complex heat exchanger behavior. For instance, in plate heat exchangers with intricate patterns of heat transfer surfaces, CFD analysis can reveal the impact of these patterns on performance. Engineers can then optimize these designs for maximum heat transfer efficiency.
In addition to its analytical capabilities, CFD analysis contributes to significant cost savings. Traditional heat exchanger optimization often involves building physical prototypes, conducting experiments, and making design iterations based on the results. These processes are time-consuming and costly. CFD analysis, on the other hand, reduces the need for physical prototypes and minimizes the expenses associated with experimentation. It is particularly advantageous when dealing with high-pressure and high-temperature systems where safety considerations are paramount. By using CFD simulations, engineers can avoid the risks associated with physical experiments in such challenging conditions. Ultimately, CFD analysis translates into both time and financial savings, making it an attractive choice for industries focused on efficiency, cost-effectiveness, and safety.
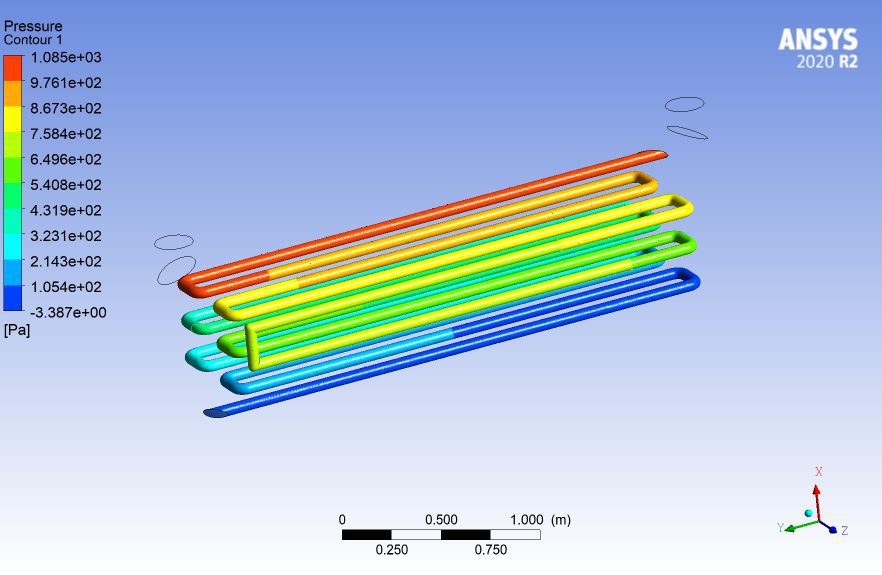
Setting up a CFD Analysis for Heat Exchangers
Setting up a CFD analysis for heat exchangers is a systematic process that requires careful planning and attention to detail. It involves defining the problem, specifying the geometry of the heat exchanger, establishing boundary conditions, and selecting appropriate numerical methods. Let’s delve into the steps required to prepare for a CFD analysis.
The first step is defining the problem. Engineers must clearly articulate the goals of the analysis. Are they aiming to enhance heat exchanger efficiency, optimize a specific parameter, or troubleshoot a particular issue? This initial step helps set the direction for the analysis and guides subsequent decisions.
Next, the geometry of the heat exchanger must be defined. This includes specifying the dimensions, shape, and layout of the heat exchanger. For example, in a shell-and-tube heat exchanger, engineers need to detail the dimensions of the tubes, shell, and baffles. The accuracy of this step is critical as it directly affects the precision of the CFD analysis.
Boundary conditions are a crucial aspect of CFD analysis. Engineers must establish the environmental conditions surrounding the heat exchanger, such as inlet and outlet temperatures, fluid flow rates, and pressures. These conditions mimic the real-world operating environment and are essential for the accuracy of the simulation. The choice of boundary conditions depends on the specific application and the goals of the analysis. It’s imperative to select conditions that align with the heat exchanger’s actual operating conditions.
Selecting appropriate numerical methods is another critical aspect of setting up a CFD analysis. Engineers need to choose the mathematical equations and algorithms that will be used to simulate fluid flow and heat transfer within the heat exchanger. The selection depends on the complexity of the problem, the available computational resources, and the desired level of accuracy.
The final steps in preparing for a CFD analysis involve mesh generation and model selection. Mesh generation is the process of dividing the geometry into smaller elements to facilitate computation. The finer the mesh, the more accurate the results, but it also demands greater computational resources. Engineers must strike a balance between accuracy and computational efficiency. Model selection involves deciding which physical and mathematical models will be used to describe fluid behavior. This choice is based on the type of fluid involved, the flow regime, and the specific requirements of the analysis.
Once these preparatory steps are completed, engineers are ready to proceed with the CFD simulation. It’s important to note that the accuracy of the analysis hinges on the diligence with which these initial steps are executed. A well-defined problem, accurate geometry, realistic boundary conditions, suitable numerical methods, and a well-structured mesh are all essential for a successful CFD analysis of heat exchangers.
Parameters and Variables in CFD Analysis
In the realm of CFD analysis for heat exchangers, numerous parameters and variables play a pivotal role in shaping the results and the overall accuracy of the simulation. These parameters encompass the characteristics of the fluids involved, the geometry of the heat exchanger, and the operating conditions. Understanding and defining these parameters correctly is essential for obtaining meaningful and relevant results.
Fluid properties are a fundamental set of parameters in CFD analysis. These properties include density, viscosity, thermal conductivity, and specific heat capacity. Accurate knowledge of these properties for both the hot and cold fluids is essential for the fidelity of the simulation. Deviations from real-world fluid properties can lead to misleading results and incorrect conclusions. Therefore, engineers often conduct experiments or rely on established data sources to ensure that the chosen fluid properties are accurate and representative of the actual fluids in the heat exchanger.
Flow rates are another critical parameter. The rates at which hot and cold fluids enter and exit the heat exchanger significantly affect its performance. In CFD analysis, these flow rates are defined as boundary conditions, specifying the mass flow rate or volumetric flow rate for each fluid stream. It’s essential to choose flow rates that match the heat exchanger’s operational conditions. Accurate representation of these conditions ensures that the CFD analysis aligns with the real-world scenario.
Temperature differentials are inherent to heat exchangers. The effectiveness of a heat exchanger depends on the temperature difference between the hot and cold fluids. This parameter must be specified accurately in the CFD analysis to model heat transfer correctly. Engineers need to define the inlet and outlet temperatures for both fluid streams, as well as any variations within the heat exchanger.
The type of heat exchanger is a critical variable in CFD analysis. Different heat exchanger types, such as shell-and-tube, plate, or finned-tube, exhibit unique characteristics. The geometry, flow patterns, and heat transfer mechanisms vary significantly between these designs. Therefore, the type of heat exchanger must be precisely defined to ensure the CFD analysis accurately represents the specific configuration being analyzed.
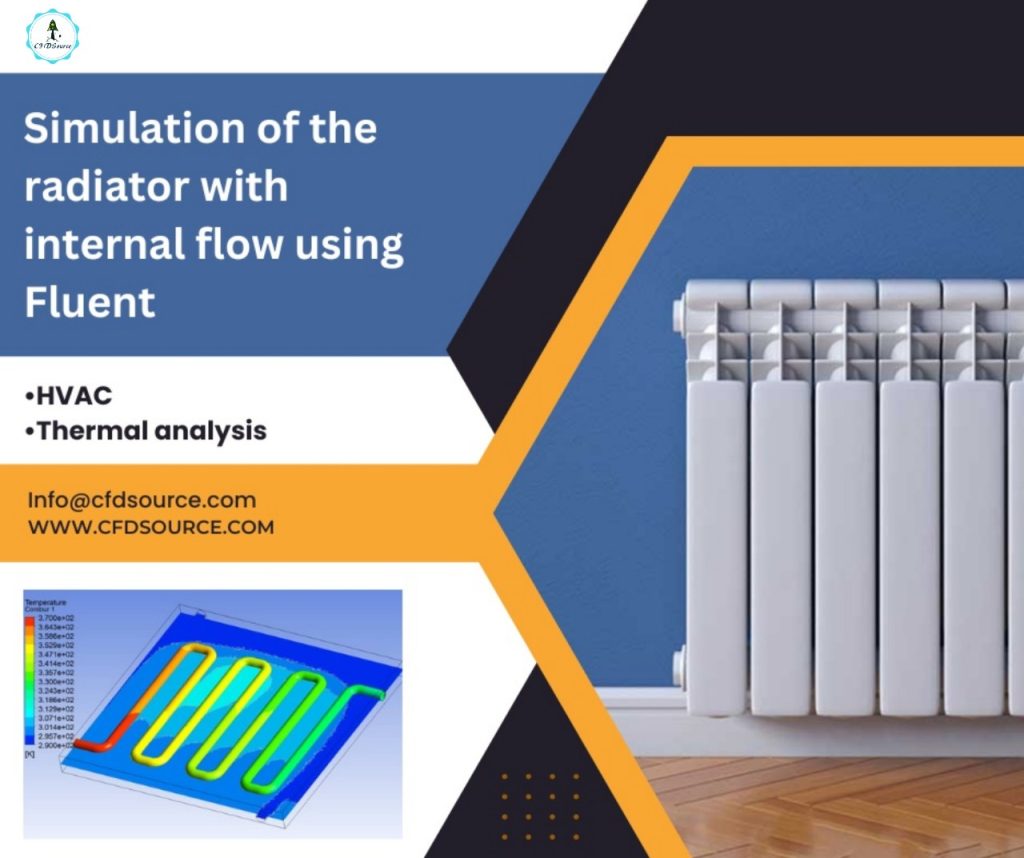
Finally, the operating conditions and environmental factors influence CFD analysis. Parameters like pressure, humidity, and ambient temperature can impact the behavior of fluids within the heat exchanger. Engineers must account for these factors in the simulation to ensure it accurately reflects the real-world operation of the heat exchanger. In summary, the correct definition and representation of parameters and variables in CFD analysis are essential for obtaining meaningful and accurate results. Fluid properties, flow rates, temperature differentials, heat exchanger type, and operating conditions all influence the simulation’s fidelity and its ability to guide design and operational decisions.
Conclusion
In conclusion, the field of Computational Fluid Dynamics (CFD) analysis in the realm of heat exchangers is a captivating journey into the heart of fluid dynamics and heat transfer. Understanding heat exchangers, recognizing their significance, and optimizing their performance are essential steps in improving energy efficiency and reducing operational costs across various industries. The benefits of CFD analysis, including its ability to simulate fluid behavior, guide design modifications, and avoid costly experiments, are pivotal in today’s engineering landscape.
The process, from setting up a CFD analysis to interpreting its results and optimizing heat exchanger performance, is intricate but rewarding. Real-world applications of CFD span across a multitude of industries, demonstrating the versatility and importance of this tool. Challenges exist in terms of complex simulations, model accuracy, and turbulence modeling, but they do not deter the use of CFD. The future of CFD analysis promises advancements in software, algorithms, and integration with other engineering tools, making it even more accessible and powerful. Furthermore, the application of artificial intelligence and machine learning will streamline the analysis process. Overall, the journey through CFD analysis in heat exchangers is a testament to human innovation and our commitment to energy efficiency, sustainability, and technological advancement.