CFD Analysis of Propellers: When it comes to propellers, whether they’re used in marine applications or aviation, optimizing their performance is crucial. Computational Fluid Dynamics (CFD) analysis has become an invaluable tool in achieving this optimization. This article explores the world of CFD analysis in the context of propellers, shedding light on its significance, benefits, processes, and the parameters it examines.
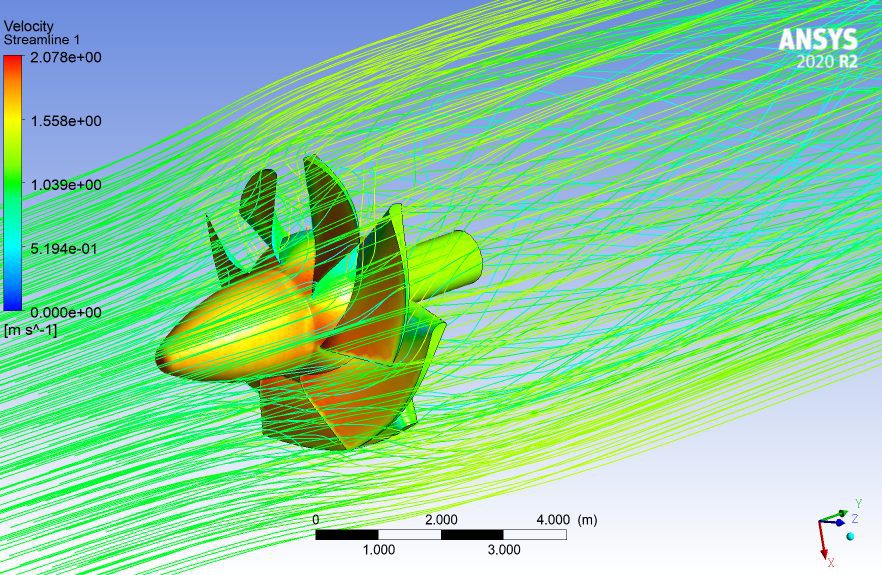
Introduction to CFD Analysis
Computational Fluid Dynamics, commonly referred to as CFD, is a dynamic field that has revolutionized the way engineers and designers approach fluid-related challenges. CFD is, at its core, a numerical approach that allows us to understand and predict fluid behavior. It plays a crucial role in various industries, including aerospace, automotive, and marine engineering. CFD uses mathematical equations to simulate and analyze fluid flows, providing valuable insights into the complex dynamics of fluids.
By breaking down fluid behavior into numerical data, engineers can make informed decisions regarding design, efficiency, and performance. CFD has become indispensable in the modern engineering world, where precision and optimization are paramount. It’s a tool that empowers engineers to explore the complexities of fluid dynamics and design solutions that were once deemed unattainable.
Understanding Propellers and Their Importance
Propellers, though seemingly simple in design, are the unsung heroes of the transportation industry, whether they’re propelling ships through vast oceans or aircraft through the skies. They consist of rotating blades that harness the power of fluid dynamics to generate thrust. The fluid medium can be air for aircraft or water for marine vessels. The key to their efficiency lies in their ability to create a pressure difference in the surrounding fluid.
As the blades rotate, they manipulate the fluid, generating forward thrust that propels the vehicle. The importance of propellers cannot be overstated; they are the driving force behind various modes of transport, ensuring that ships sail smoothly and aircraft soar through the skies. In essence, they are the heart of transportation, and improving their design is pivotal for enhancing performance, fuel efficiency, and environmental sustainability.
The Need for CFD Analysis in Propeller Design
The design of propellers is a complex task due to the intricate fluid dynamics involved. Creating an efficient propeller is far from a straightforward process; it requires meticulous analysis and optimization. This is where Computational Fluid Dynamics (CFD) analysis steps in to offer a solution. Without CFD, designers would rely on physical prototypes and extensive testing, which can be time-consuming and expensive. CFD bridges this gap by providing a virtual environment where propeller designs can be rigorously examined.
It allows engineers to visualize how fluids interact with propeller blades, identifying areas for improvement. With CFD, the design process becomes more streamlined and cost-effective, ultimately leading to propellers that offer enhanced performance and efficiency. By utilizing CFD, designers can refine propeller designs before a physical prototype is even created, saving time, money, and resources.
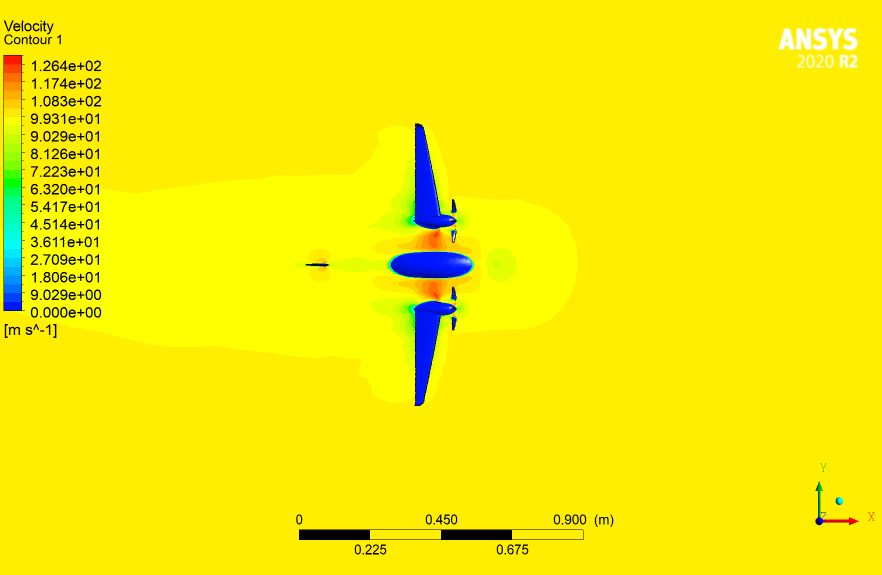
Benefits of CFD Analysis
The adoption of CFD analysis in propeller design offers a multitude of benefits that extend beyond the realm of efficiency. One of its most significant advantages is the improvement of propeller design, leading to enhanced performance. Engineers can fine-tune propeller geometry and optimize blade profiles, ensuring that the propeller operates at its peak efficiency. This results in reduced fuel consumption and increased thrust, factors that are vital for both the aviation and marine industries. CFD analysis also brings cost savings, as it reduces the need for extensive physical testing and prototyping.
With CFD, designers can explore numerous design variations without the need to create multiple physical prototypes, saving both time and resources. Furthermore, CFD allows for a more in-depth understanding of the fluid dynamics around the propeller, which can lead to noise reduction, an essential factor in both marine and aviation environments. In summary, the benefits of CFD analysis encompass improved efficiency, reduced costs, and enhanced performance, making it an indispensable tool in propeller design and optimization.
The CFD Analysis Process
The CFD analysis process is a structured and systematic approach that allows engineers to gain insights into fluid dynamics and its impact on propeller performance. It consists of three primary phases: pre-processing, simulation, and post-processing. Pre-processing involves setting up the groundwork for the analysis. Engineers define the geometry of the propeller and create a mesh, which is a division of the geometry into smaller elements to facilitate analysis. Boundary conditions are also established, specifying the operating conditions such as flow velocity and temperature.
The simulation phase is the heart of the CFD analysis, where fluid flow equations are solved. This step utilizes powerful computational algorithms to simulate the behavior of fluids around the propeller. The final phase, post-processing, involves the interpretation of simulation results. Engineers analyze data related to velocity, pressure, and temperature distributions, and visualize the flow patterns to draw meaningful conclusions. In essence, the CFD analysis process is a powerful tool that empowers engineers to comprehend the intricate fluid dynamics that impact propeller performance.
Tools and Software for CFD Analysis
To effectively conduct CFD analysis on propellers, engineers rely on a variety of specialized tools and software. These software packages are essential for setting up, simulating, and post-processing the analysis. ANSYS Fluent, a widely used CFD software, offers a comprehensive suite of tools for fluid flow simulations. Its capabilities range from simple flow analysis to complex multiphase and combustion simulations, making it versatile for different propeller design scenarios.
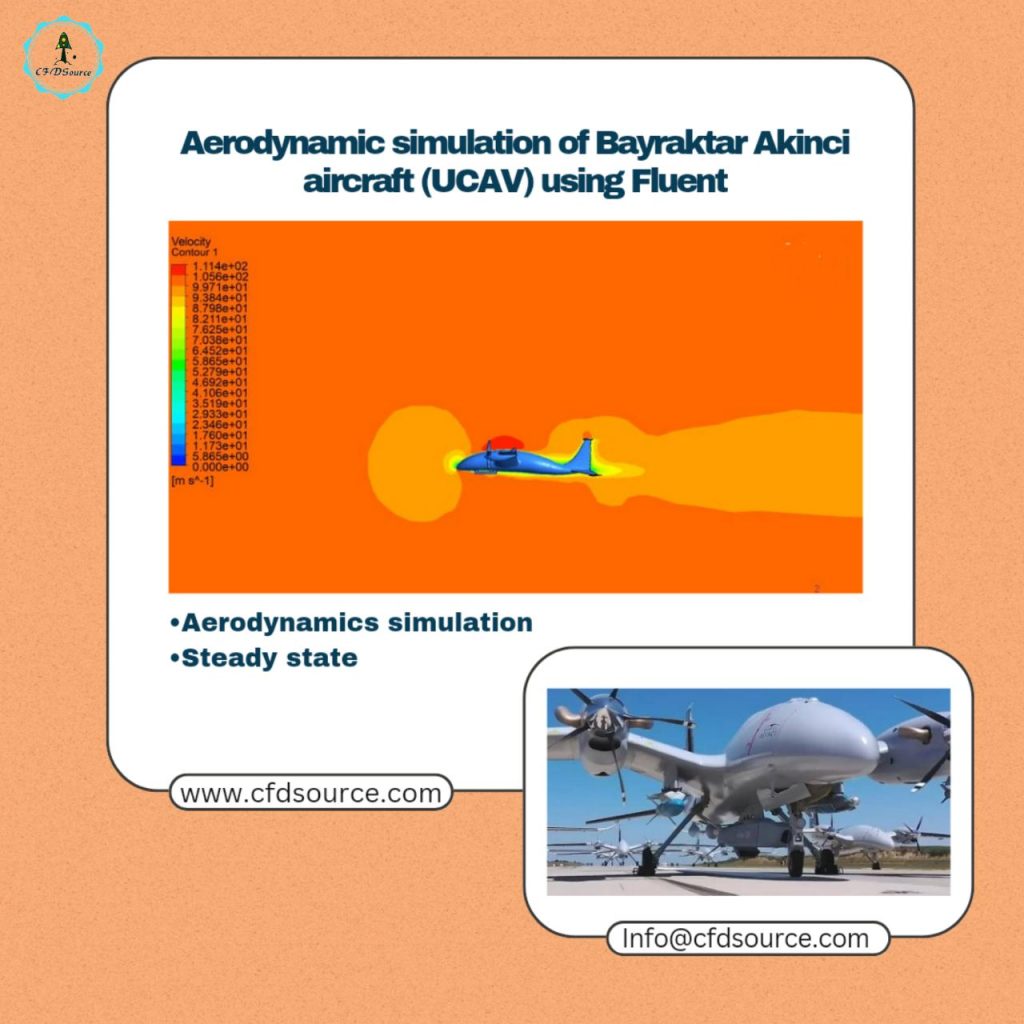
OpenFOAM, on the other hand, is an open-source CFD software that allows engineers to customize and tailor simulations to their specific needs. It provides a flexible platform for propeller analysis and is popular in the research community. COMSOL Multiphysics is another powerful tool that combines CFD with other physics simulations, enabling a holistic approach to propeller design. These tools, among others, are the backbone of CFD analysis, providing engineers with the means to model, simulate, and analyze fluid behavior around propellers, leading to optimized designs.
Steps in Conducting CFD Analysis on a Propeller
Conducting CFD analysis on a propeller is a systematic process that involves several essential steps. First, engineers create a 3D model of the propeller’s geometry. This model accurately represents the shape and dimensions of the propeller blades. Subsequently, mesh generation is performed. Meshing involves dividing the geometry into smaller elements, known as mesh cells or elements. This step is critical because it dictates the accuracy of the analysis; a finer mesh provides more precise results. The next step is defining boundary conditions. Engineers specify factors like flow velocity, temperature, and pressure at the propeller’s inlet and outlet. These conditions mimic real-world scenarios.
The core of the analysis is solving the fluid flow equations. Using specialized CFD solvers, engineers simulate the fluid behavior around the propeller. Finally, post-processing comes into play. Here, engineers interpret and visualize the results of the simulation. They analyze parameters such as velocity and pressure distributions to gain a deeper understanding of how the propeller interacts with the surrounding fluid. These steps, when executed meticulously, provide engineers with invaluable insights for propeller design optimization.
Parameters Analyzed in CFD
CFD analysis delves into several key parameters when examining propellers, each of which plays a crucial role in assessing their performance and efficiency. The first parameter is thrust, which evaluates the propeller’s ability to generate forward force. Efficiency is another critical factor, determining how effectively the propeller converts power into thrust. For propellers, minimizing energy waste is pivotal for achieving peak performance. Cavitation is a phenomenon that is closely scrutinized. It involves the formation and collapse of vapor bubbles due to low pressure zones.
CFD helps identify areas prone to cavitation, which can be damaging and reduce propeller efficiency. Vibration is also analyzed, as it affects the structural integrity of the propeller and can lead to operational issues. The vibrations generated by the interaction of the fluid with the blades need to be minimized for safety and performance reasons. In summary, CFD analysis focuses on these parameters to fine-tune propeller designs, ensuring they operate at their optimum, delivering efficient thrust, and minimizing the detrimental effects of cavitation and vibration.
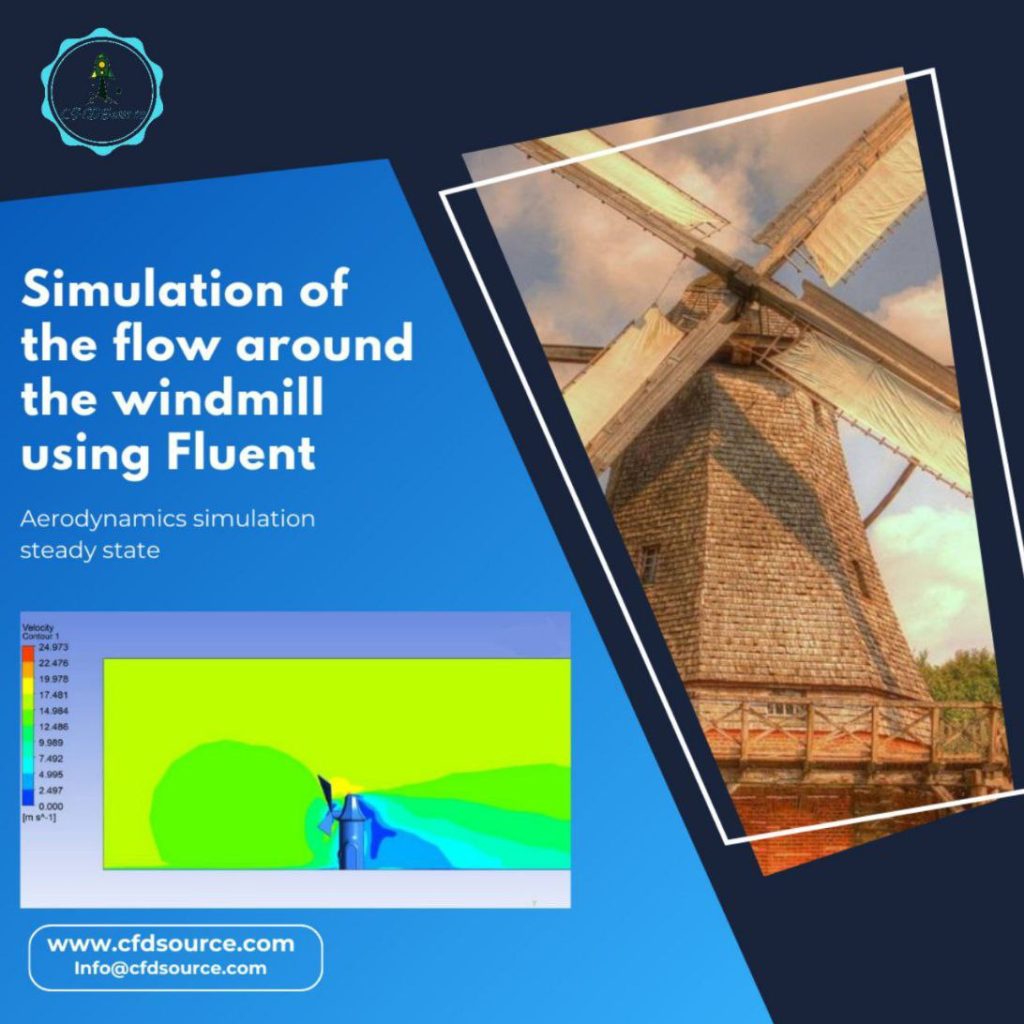
Case Studies
When considering the real-world impact of CFD analysis on propellers, it’s enlightening to explore case studies that highlight its effectiveness. One notable area where CFD has made significant contributions is in the design of marine propellers. By simulating the complex interaction of water with propeller blades, CFD has allowed engineers to develop highly efficient and low-noise marine propellers. These designs not only increase the efficiency of ships but also contribute to the reduction of noise pollution and, by extension, the environmental impact.
In the aviation industry, CFD analysis has played a pivotal role in optimizing aircraft propellers. Engineers have used CFD to enhance the performance of these crucial components, leading to improved fuel efficiency and minimized noise levels. Case studies are instrumental in showcasing the tangible benefits of CFD analysis, demonstrating its role in shaping more efficient, environmentally friendly, and quieter transportation methods.
Challenges and Limitations of CFD Analysis
While CFD analysis offers numerous advantages in propeller design, it’s essential to acknowledge its challenges and limitations. One of the primary challenges is the demand for substantial computing resources. Conducting high-fidelity CFD simulations often requires powerful computers and dedicated computational clusters. Additionally, the process can be time-consuming, especially when dealing with complex geometries. Errors can occur if the CFD simulation is not set up correctly, which can lead to misleading results.
Furthermore, the accuracy of CFD simulations depends on the quality of the mesh and boundary conditions, which can be challenging to define accurately. It’s also important to note that CFD analysis should complement, not replace, experimental testing. Physical testing remains crucial for validation and fine-tuning of propeller designs. In summary, CFD analysis, while powerful, has challenges related to computing resources, accuracy, and the need for physical testing to ensure reliable results.
Future Trends in CFD Analysis for Propellers
The future of CFD analysis for propellers holds exciting possibilities. As computing power continues to advance, CFD simulations will become even more detailed and accurate. This means that engineers will have access to highly precise data, allowing for a deeper understanding of propeller performance. Moreover, the integration of artificial intelligence (AI) and machine learning (ML) into CFD software will enhance the optimization process. AI and ML can help identify patterns in large datasets, suggesting design improvements and reducing the time required for manual adjustments. Additionally, the trend toward sustainability in transportation will drive further developments in CFD.
Engineers will use CFD analysis to create eco-friendly propellers that offer improved performance and reduced environmental impact. The future may also witness an increase in the use of virtual reality (VR) and augmented reality (AR) technologies in propeller design. Engineers could visualize CFD results in immersive environments, gaining more intuitive insights into fluid dynamics. These future trends in CFD analysis promise to revolutionize propeller design, leading to more efficient, environmentally conscious, and high-performance solutions.
Conclusion
In conclusion, CFD analysis is a transformative tool for propeller design, providing engineers with the means to optimize efficiency, reduce costs, and enhance performance. It plays a critical role in understanding the complexities of fluid dynamics and their impact on propellers in both marine and aviation applications. The ability to create virtual environments for simulation eliminates the need for extensive physical testing, resulting in significant cost savings and a streamlined design process.
CFD has allowed designers to improve propeller geometry and enhance blade profiles, leading to reduced fuel consumption and increased thrust. While CFD analysis comes with its own challenges and limitations, its benefits far outweigh the drawbacks. As computing power and AI technologies continue to advance, the future of CFD analysis for propellers looks promising, offering more precise simulations and sustainable design solutions. The propeller industry will undoubtedly continue to leverage the power of CFD to create more efficient, eco-friendly, and high-performance propellers, driving innovation and progress in the world of transportation.